RECOMMENDED PRACTICE FOR STORAGE OF CEMENT.
01) INTRODUCTION
Cement is the most important material in construction activities and its used in every construction site all over world.
Cement is a binding material and react with the water during making concrete.
|
---|
![]() |
• OPC 53 Grade • OPC 43 Grade • OPC 33 Grade • IS 1489 Part-1 (Flyash Based) • IS 1489 Part-2 (Calcined clay based) |
---|
|
---|
|
![]() |
---|
04) RANDOM VISUAL INSPECTION
Following information statutorily printed on cement bags should be checked.
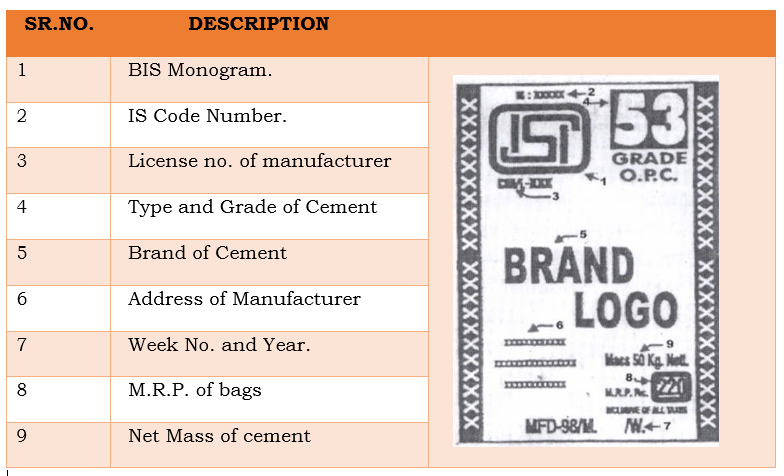
.
05) WEATHER-PROOF CEMENT STORAGE SHED
- The walls must be leak proof, Brick masonry walls must be plastered with cement-sand plastered (waterproof) on the external face with 2 coats.
- The roof must preferably be of reinforced concrete construction overlaid with a waterproofing course. AC/GI sheet roof construction may be used provided they are leakproof.
- The floor must be raised by at least 40 cm above the ground level to prevent any inflow of water. The flooring may consist of a 15 cm thick concrete slab or layer of dry bricks laid in two courses over a layer of earth consolidated to a thickness of 15 cm above the ground level. Although not shown on the drawing, the outside ground is drained away from the building to prevent accumulation of rainwater in its vicinity. All these precautions ensure that the floor will remain dry.
- For further protection, cement bags should be stacked at least 10-20 cm clear above the floor by providing wooden battens and planking arrangements.
- Preferably, the plinth should be high enough for a lorry to back conveniently to the door so that, the chassis and the building floor is almost at the same level, thus making loading and unloading of bags very easy.
- Windows provided, if any, should be very few and of small size, and normally kept closed tightly to prevent entry of atmospheric moisture from outside. The door should also be tight and always kept closed unless in use.
.
06) ESSENTIAL PRECAUTIONS FOR STACKING OF CEMENT BAGS
• Type & Grade of cement. • Name of the manufacturer. • Date of manufacturing (week and year). |
![]() |
---|
- These boards should be rotated accordingly.
- Aisles should be clearly marked between the stacks to have a clear access to all the stacks and minimum 600 mm should be maintained between two stacks.
- While using, cement bags should be opened by removing thread and not by cutting the bags.
• Yellow sign board for cement manufactured between the oldest and the latest. Green sign board for latest manufactured cement.
.
LEGEND:
-
- Red: Oldest manufactured cement bags
- Yellow: Cement bags manufactured between oldest and latest
- Green: Latest manufactured cement bags
- “A”: Planks and Tarpaulin
- “B”: Wooden Battens
- “C”: P.C.C. Flooring
- “D”: Rubble Soling
- “E”: Load Bearing Wall
07) CEMENT IN BULK
In major projects and in RMC plants cement is received in bulkers as the consumption of cement is very high on a day-to-day basis.
These are storage solutions for any capacity and size could be manufactured.
Technical design content should include: process flow, equipment selection, dust removal system and material level control, etc.
Cement steel silo with diameter below 10m should apply gravity feed mechanic, and the bottom slope should more than 45°.
Flat bottom steel silo should apply screw conveyor for cement transmission or other facilities.
The dust pelletizing system of a cement silo includes the selection and layout of dust removal equipment.
Dust removal design should be chosen according to the following parameters: filter should not be less than 24 squares when the silo capacity is under 500 t, above 500 t should choose according to the specific tonnage multiplied by the coefficient of 0.05.
Dust collecting equipment should be open layout. It can be set at the top of the silo, while it is pretty to be installed at the bottom of the silo for centralized deducting.
The butterfly valve should be set on the bottom of centralized dedusting equipment.
The design of dust removal system should according to the opening order and operating requirements.
Quantity of cement available in silo shall be checked daily. Cement shall be fed into the silo only after confirmation of availability of enough space to accommodate the fresh batch of cement, and minimum daily required quantity of cement shall always be maintained.
